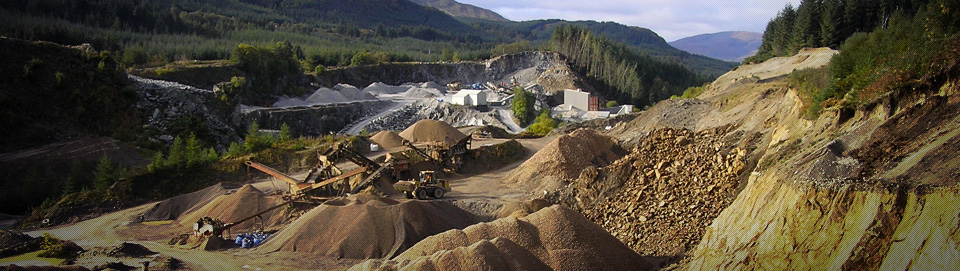
Highland Lime produces industrial filler and animal feed additive products from the limestone deposits on site. As an essential service provider for animal feed products, the Mill House remained in full operation throughout the Covid-19 Pandemic.
The old system was not very flexible and relied on a lot of operator input to produce the products with a plant that was prone to outages and constant housekeeping. Product storage was limited and the buildings also required replacing. Numerous options had been considered for replacing and siting the plant, but, due to the peculiar layout of the quarry, finding a suitable location for a new milling plant to suit future quarry operations, proved difficult. It was finally decided that a complete refit of the existing buildings would be the best long-term option.
To modify the system, additional product storage was installed, so that stocks could be increased and the impact to our customers minimised. A 1000 tonne 7.8m diameter silo was erected on new foundations prepared by Leiths Civil Engineering Division. In addition to this mammoth silo for limestone filler, an additional six 120 tonne silos were built in line with the large one. All seven silos have telescopic loading socks, 6 of which are designed to be able to load tankers and tipper bodies, whilst eliminating loading dust.
With these 7 new silos in place, buffer stocks could be increased by installing new blowing systems from the old system. Once in place, this allowed the old hoppers, and some parts of the building, to be removed. Leiths newly formed Project team, headed by Edwin Connor carried out these enabling works, erected the new structural steel that had been designed and fabricated at Leiths’ Rigifa Fabrication Workshop. In parallel with these works, the Civil Engineering Division were pouring foundations for the new building that would almost entirely enclose what had been there before.
With the 1000t silo full of limestone filler, modifications to the mill itself could be made, whilst still producing animal feed products on the old system. The old mill system was dismantled and a new feed hopper installed in its place. The hopper was slotted into a space between the mill and Baghouse with less than 10mm to spare. A new mill fan, separator cyclone, and VBC divorced classifier from Bradley Pulveriser were positioned above the mill. It was now possible to erect the new building over what still remained of the old system and make the area weather-tight.
The rebuild of the plant gave the opportunity to control energy use on the site. Variable speed drives have been installed on the many of the drives within the system to allow the motors to run at optimum performance maintaining our commitments under the Energy Management System: ISO 50001. The additional control also has the added benefit of fine tuning the milling operation to produce additional products as and when required.
The remnants of the old buildings are now being removed from within the new building, to make space for future expansion of the facility.