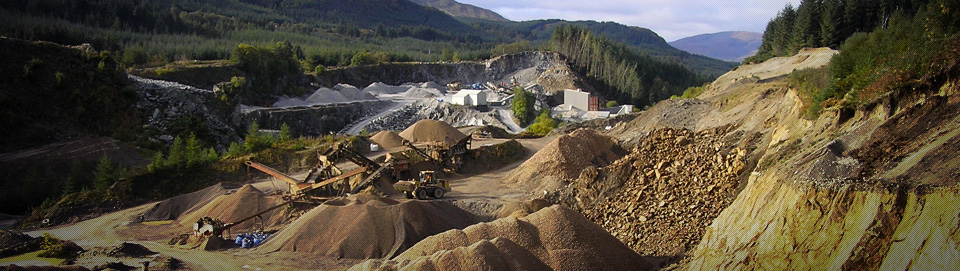
Situated near Cove, Aberdeen, Blackhills Quarry has been operational within the Leiths Group since the late 70’s. During this period, we have extracted over 15 million tonnes of high-quality granite. The quarry produces a wide range of construction aggregates as well as rock armour, ready mixed concrete, and asphalt materials.
Both the location of the quarry, which is only 200m from the North Sea, and the attrition of the particularly hard granite, means that wear and corrosion play a significant part in plant longevity of this busy quarry. As a key producer within the Leiths Group, the time was right to renew our fixed crushing and screening plant to support our onsite concrete and asphalt plants.
The upgrade work started with installing a new reclaim tunnel system which feeds primary crushed rock to a new 50t surge hopper that in turn feeds an Allis Chalmers 1645 secondary crusher.
The secondary crushed material is then fed over a Sandvik SC2472 Circular Motion Screen which splits the rock into three size fractions plus a Type 1 Sub Base. From the large holding hoppers below, the rock is fed into three Tertiary H36 Allis Chalmers cone crushers with a fourth Quaternary H36 crusher to balance production requirements of specific aggregate sizes when needed. These reliable and efficient crushers produce aggregates ranging in sizes from 32mm down to dust. From these crushers the material is conveyed up to our final screening station where the aggregates are passed over three large Sandvik (1x SC2462 and 2x SC2472) screens which sort the aggregates into their respective size fractions storing in large hoppers below.
From these holding hoppers the aggregates can be either fed directly into the asphalt plant or loaded into dumpers or road going tippers for stocking or onward delivery to customers.
As part of our continuing commitment to energy efficiency, every effort was made to design in the most energy resourceful technology throughout the new processing plant.
Variable speed drives were used wherever energy savings can be made. Control logic maintains the plant at an optimum throughput to minimise stop-start running and the need to run empty plant and machinery. Feeding the freshly crushed aggregates and dust directly into the asphalt plant from the storage hoppers optimises fuel consumption and production throughout, as well as emitting less carbon into the atmosphere.
This significant project demonstrates our ongoing commitment to investment and ensures we continue to exceed the elevated levels of quality and service that our customers have come to expect.